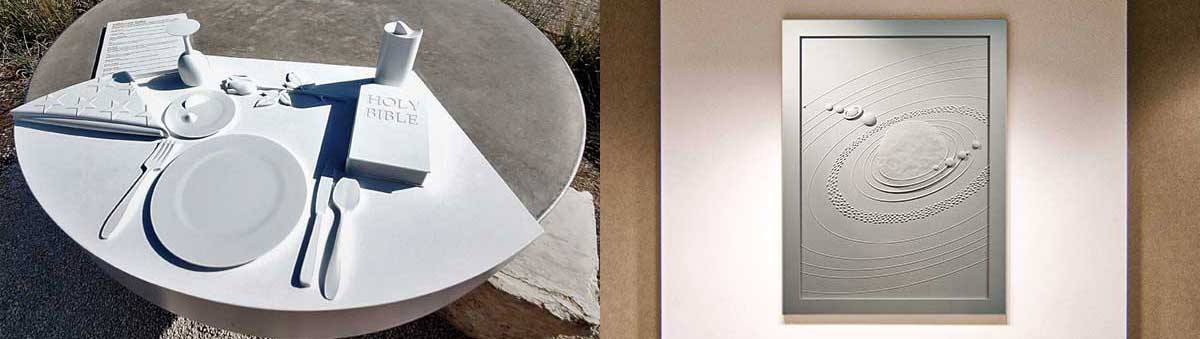
At its core, thermoforming is a process that transforms solid surfaces into durable, three-dimensional shapes through precise heating, forming, and cooling techniques. Whether you’re looking to create fluid curves, seamless corners, or custom architectural elements, thermoforming takes flat design and bends it to your will – literally.
We see thermoforming as more than just shaping materials; it’s about pushing creative boundaries with advanced tools and expert craftsmanship. Using ovens, vacuum presses, molds, and CNC routers, we bring your vision to life in striking, functional form.
The applications are as varied as they are stunning. Curved countertops, cascading waterfall edges, 3D wall cladding, sculpted furniture, seamless reception desks, integrated sinks – thermoforming empowers designers to defy flat-panel limitations and build truly dynamic environments. This process is ideal for industries like hospitality, healthcare, commercial, marine, and retail spaces where aesthetics must also deliver function.
View Complex Thermoforming in action.
While thermoforming unlocks fluid form and design freedom, it works best within certain parameters:
• Material + thickness: Typically 6mm to 12mm solid surface materials
• Minimum bend radius: 50mm (2 inches)
• Integrate curved solid surfaces with metal, wood, stone, and glass for an extraordinary effect
• Color & finish options: huge variety of solid surface colors and options
Traditional flat fabrications often come with limitations—sharp corners, rigid layouts, and visible seams. Thermoforming, by contrast, enables smooth, contoured surfaces that are both visually striking and highly functional. It removes joint lines and allows for ergonomic shapes that enhance user experience and elevate overall design. These surfaces are also exceptionally durable, repairable, and moisture-resistant, making them perfect for high-traffic or demanding environments.
Thermoforming isn’t one-size-fits-all, it’s a customized process tailored to your project’s unique specifications. Here’s how it works:
1. Submit your ideas – sketches, drawings, or mood boards are welcome
2. Consultation – we assess feasibility, materials, and timeline
3. Mold creation – custom molds are crafted using wood, foam, or other substrates
4. Forming – materials are precisely heated and shaped
5. Finishing touches – surfaces are cooled, trimmed, and polished
6. Delivery – the final product is ready for installation or integration
Project timelines can vary from a few hours to several days depending on complexity. While the setup and tooling costs are higher than traditional fabrication, the end result offers unmatched design flexibility and long-term value.
If you’re looking to transform your next design with seamless curves and sculpted beauty, we’re ready to help.